In-wheel-drives with external rotor technology
- Wolfgang A. Haggenmüller
- May 8
- 8 min read
The automotive industry is developing rapidly, especially in the field of electromobility. One of the most innovative developments is in-wheel drives, in which electric motors are installed directly in the wheels of a vehicle. This technology offers numerous advantages over traditional centralized drive systems by eliminating the need for mechanical components such as drive shafts, differentials, and transmissions. A special variant of this is the outrunner motor, which is characterized by its special design and technical features. In the following, the structure, the functionality as well as the advantages and disadvantages of this technology are explained in detail, supplemented by technical aspects such as magnetic field curves, cooling strategies, material selection and practical applications in automotive engineering.

In-Wheel-Drives
An in-wheel drive, also known as a wheel hub motor, is an electric motor that is integrated directly into the wheel of a vehicle. Unlike conventional drives, where power is transmitted to the wheels via a central drive unit and a cardan shaft or transmission, in-wheel motors drive each wheel individually. This eliminates numerous mechanical components such as differentials, transmissions and drive shafts, which can save space and weight
Design and operation of in-wheel drives with external rotor technology
The basic idea of an in-wheel drive is to integrate the motor directly into the wheel hub, allowing each wheel to be driven independently. In the outrunner configuration, the rotor sits on the outside of the stator. While classic internal rotor motors place the rotor inside a fixed stator, the external rotor approach enables a larger radial dimension of the rotor. This results in an increased flywheel mass, which generates more torque at lower revs. The distribution of the magnetic flux is optimized by the larger air gap and the specific geometry of the stator windings. The rotating magnetic field in the stator induces a uniform torque in the externally mounted rotor, which ensures precise power transmission to the wheel surface. By directly controlling each wheel, modern control algorithms, such as torque vectoring, can be implemented, which significantly improves driving stability and cornering performance.
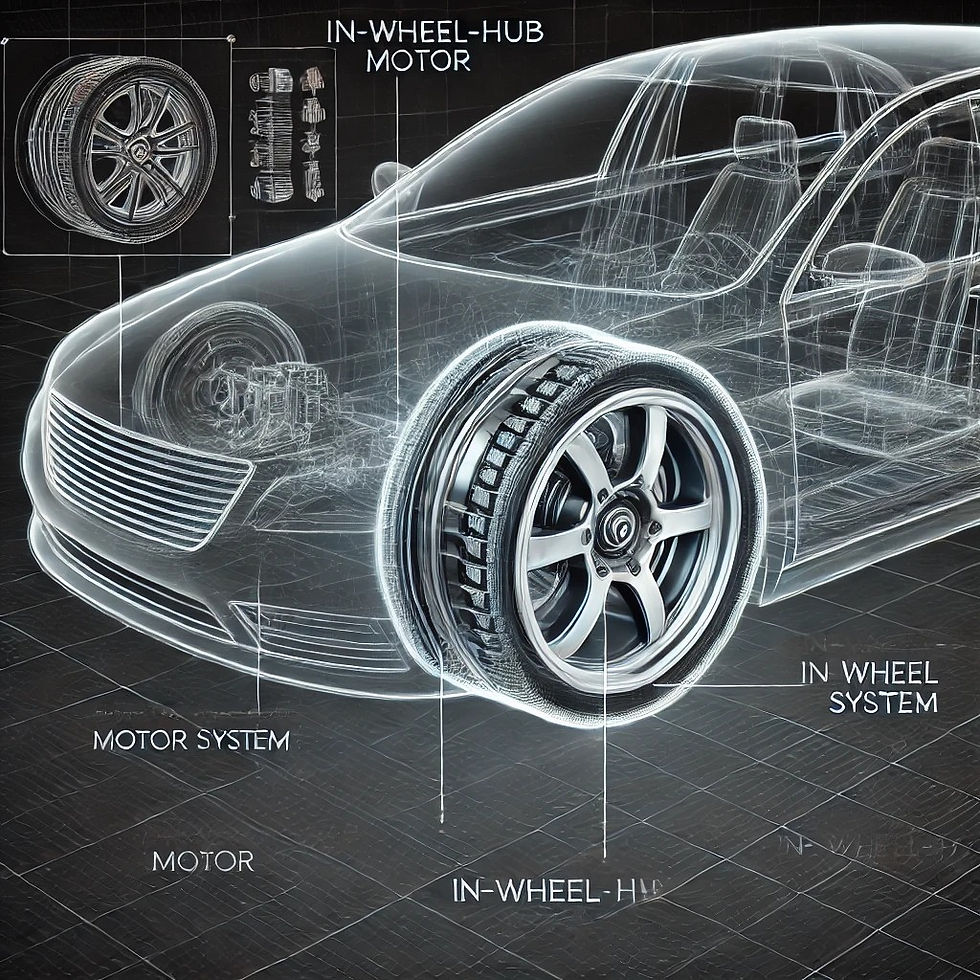
Another central technical aspect is the cooling of the in-wheel drives. Due to the compact design and integration into the wheel, special thermal challenges arise. Although the external rotor motor offers a good opportunity for passive heat dissipation due to its larger surface area, active cooling is often indispensable for high performance and continuous operation. Modern systems rely on liquid or forced air cooling to keep the temperature in the optimal range and thus ensure the efficiency and service life of the engine. The development of highly efficient cooling circuits is an essential part of advanced in-wheel technology.
The choice of materials also plays a decisive role in the optimization of in-wheel drives. The use of lightweight materials such as aluminum, high-performance plastics or composites not only enables a reduction in unsprung mass, but also contributes to improved thermal stability. High-quality magnetizable materials such as silicon steel are often used in the stator, while rare earths in the form of neodymium-iron-boron magnets can also be used in the rotor – especially in variants with permanent magnets. However, some designs deliberately avoid expensive magnets and rely on a purely reluctance-based design in order to save costs and reduce the ecological footprint.
The advantages of in-wheel drives with external rotor technology are obvious: by eliminating many mechanical transmission elements, the system becomes lighter, more compact and potentially more efficient, as energy losses are minimized. The direct control of each wheel also offers a high degree of flexibility and control, which leads to improved traction and stability, especially in dynamic driving situations. This not only allows vehicles to accelerate faster, but also to act more precisely in corners, as the torque can be distributed individually.
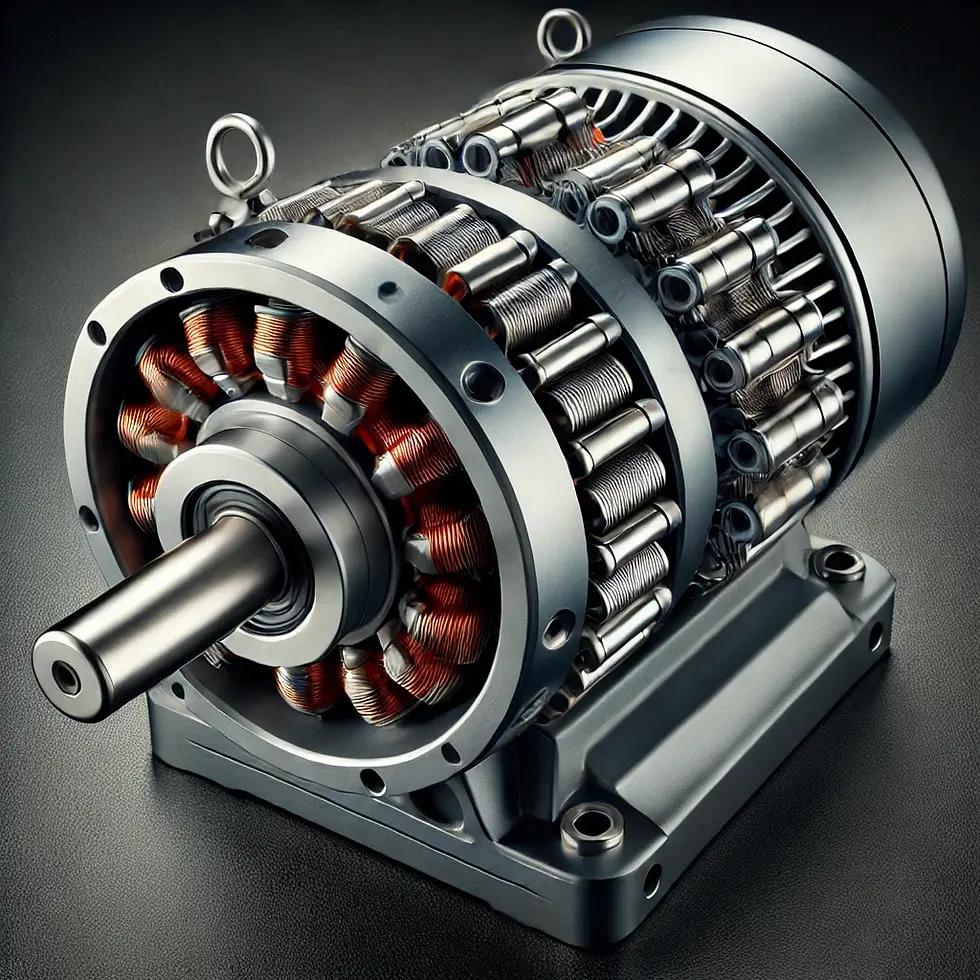
Nevertheless, there are also challenges that need to be taken into account. A major disadvantage is the increased unsprung mass, as the motors are installed directly in the wheels. This can affect handling, especially ride comfort and suspension dynamics. In addition, the precise electronic control of the individual wheel motors requires complex control algorithms and robust hardware, which leads to higher development and production costs. Integration into existing chassis and brake systems poses further technical challenges that must be overcome through innovative designs and simulation techniques.
Practical applications of in-wheel drives with outrunner technology can be found today primarily in concept vehicles and test models in the field of urban mobility. Companies such as Protean Electric and Elaphe have developed prototypes that are characterized by high maneuverability and efficiency. Lightweight, manoeuvrable electric cars and city buses in particular benefit from the decentralised drive technology, as it meets the requirements for space optimisation and individual wheel control. Some manufacturers also use this technology in electric commercial vehicles to ensure better traction under varying load conditions. The ability to adapt the drive concept to different road conditions through torque vectoring makes the in-wheel drive particularly attractive for use in vehicles operating in urban environments, where frequent stop-and-go situations and tight curves are common.
The in-wheel hubs will continue to be only a special drive in automotive applications that hardly go beyond small series. Currently, only Dongfeng vehicles with the use of wheel hub motors and the Renault R5 Turbo 3E small-series high-performance vehicle are known. . There are currently no other OEMs known to have announced plans for the application of wheel hub motors. The Dongfeng (E70 and Passion) cars with a combination of e-axle and two wheel hub motors are not yet available for the open market, but only for the taxi and ride-hailing market in certain districts.
In summary, it can be said that in-wheel drives with outrunner technology are a promising approach in modern automotive engineering. Their innovative design enables direct power transmission, optimized traction control and flexible integration into different vehicle types. Despite technical challenges such as increased unsprung mass and complex cooling requirements, they offer significant advantages in terms of efficiency, driving dynamics and space optimization. As research and development progresses, these systems could be used in a wider range of vehicles in the future and make a decisive contribution to the further development of electromobility.
DeepDrive
@DeepDrive is an innovative company in the field of electromobility that has developed a novel electric motor technology based on a twin-rotor design. This architecture promises significant improvements in efficiency, cost reduction and power density compared to conventional drive systems. The core of the DeepDrive technology is a twin-rotor radial flux motor. Unlike traditional electric motors, where the stator drives either an internal or external rotor, the stator in DeepDrive moves both an inner and an outer rotor at the same time. This design allows for more efficient use of magnetic flux and results in higher power density. Another feature is the revolutionary winding concept with distributed bar unwindings, which achieves a slot fill factor of over 80% and simplifies production. In addition, DeepDrive integrates an ultra-efficient SiC inverter optimized with innovative topology and SiC MOSFETs to reduce losses.
Technology and construction
The advantages of this technology are mainly in terms of material savings, as the motor requires 50% less magnetic material and 80% less iron compared to current electric drives, which leads to a significant reduction in weight and costs. Due to the lower use of materials and the efficient construction method, production costs can be reduced by about 30%. Vehicles with DeepDrive technology can achieve up to 20% higher efficiency in the driving cycle, either increasing the range or reducing the size of the battery required. The engines are compact and lightweight, which leads to better use of space in the vehicle. However, the technology also brings challenges. The double-rotor architecture requires precise manufacturing techniques and can make production processes more complex. In addition, the implementation of new technologies into existing vehicle platforms can present challenges, especially in terms of design adjustments and compatibility.
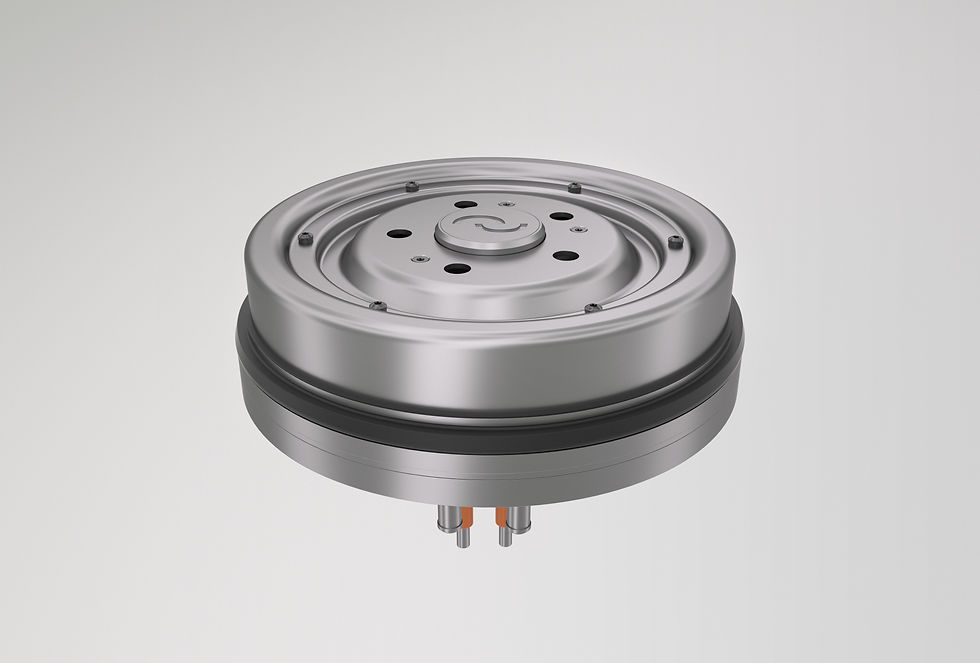
Compared to traditional electric motors, which are designed as either internal rotor or outrunner, DeepDrive's dual-rotor design offers more efficient use of magnetic flux and higher power density. In addition, the material savings in magnets and iron enable more cost-efficient production. In contrast to wheel hub motors, which are integrated directly into the wheels and often struggle with increased unsprung masses, DeepDrive offers a central drive solution that circumvents this problem.
Applications and future viability
DeepDrive is currently working with eight of the ten largest car manufacturers, with the integration of the engines into production vehicles expected in 2028. The technology is suitable for both central drive units and wheel hub drives, allowing for a wide range of applications. The combination of high efficiency, cost-effectiveness and material savings makes DeepDrive technology a promising solution for the future of electromobility.
In summary, DeepDrive technology represents a significant advance in the field of electric motors, with the potential to increase efficiency, reduce costs and promote sustainability in the automotive industry.
By-wheel motors – an alternative to in-wheel drives
Another important approach that is becoming increasingly popular is by-wheel motors. Unlike traditional wheel hub motors, which are fully integrated into the wheel hub, by-wheel motors are usually mounted on the wheels but are not integrated directly into the hub. This brings some decisive advantages.
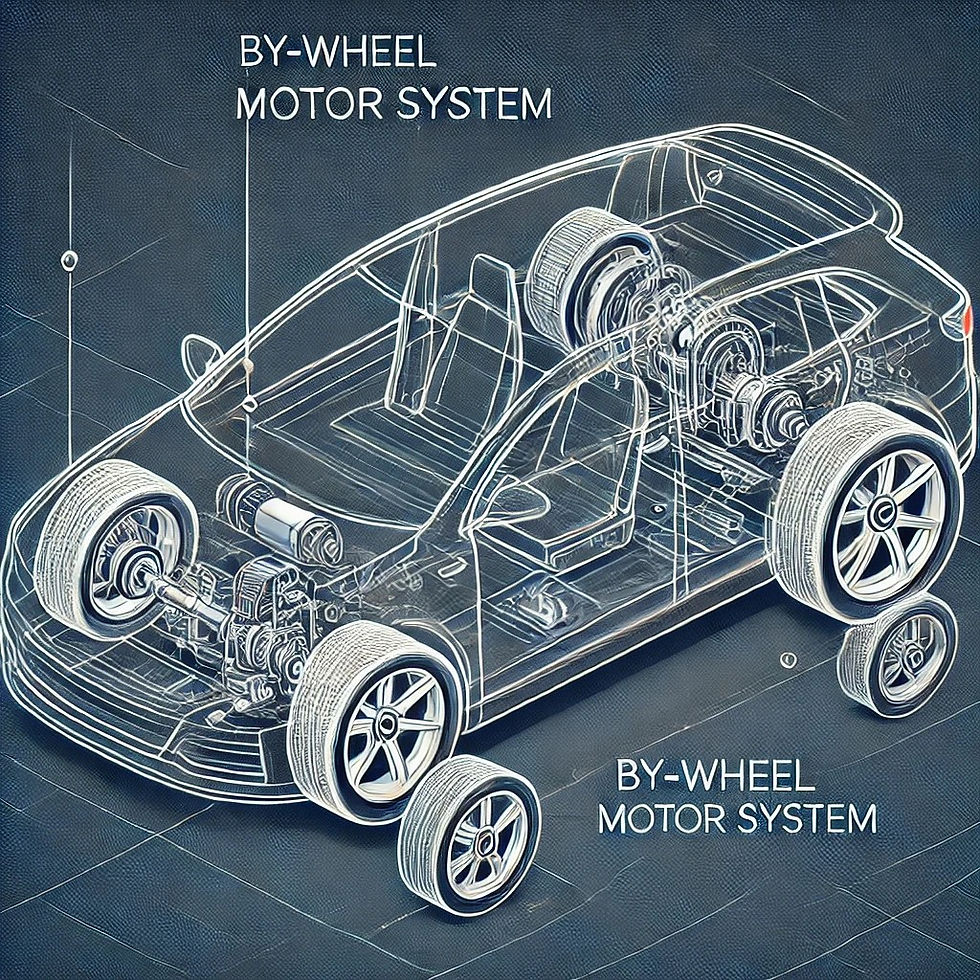
By-wheel motors offer greater reliability because they are subjected to less mechanical stress than fully integrated in-wheel drives. This makes them more robust and less susceptible to problems such as bearing failures or signs of wear. Another significant advantage is better heat dissipation. Because the motors are not fully integrated into the wheel hub, waste heat can be dissipated more efficiently, improving overall performance and motor life.
An additional advantage is the flexibility in vehicle design. By-wheel motors allow manufacturers to better adapt the vehicle architecture to different requirements, as they are not necessarily tied to a specific wheel size or design. This opens up new possibilities for optimized platforms in electric vehicle construction. In addition, these motors can offer improved traction and acceleration by working directly on the wheels, making power transmission more efficient.
By-wheel motors are increasingly being used in high-priced Chinese electric vehicles because they offer an optimal balance between performance, efficiency and integration. As more and more customers are looking for reliable and high-performance solutions, the interest in by-wheel motors has increased in recent years. Many high-priced Chinese car brands such as Yangwang, Denza, Zeekr, Lynk&Co, and Xiaomi have started to use this technology, which has led to significant growth in this segment.

Differences between by-wheel motors, in-wheel hubs and DeepDrive drives.
While classic in-wheel hub motors sit directly in the wheel hub and drive the wheel directly, by-wheel motors are located outside the wheel hub but are attached directly to the wheels. This reduces the unsprung mass, which is often seen as a disadvantage in wheel hub motors. The DeepDrive twin-rotor drive, another innovative development, differs from both concepts in that it not only offers an extremely compact design, but also maximizes efficiency and reduces the cost of materials through its double-rotor technology. In contrast to by-wheel motors, which rely on the most flexible integration possible, DeepDrive is particularly optimized for scalable vehicle platforms.
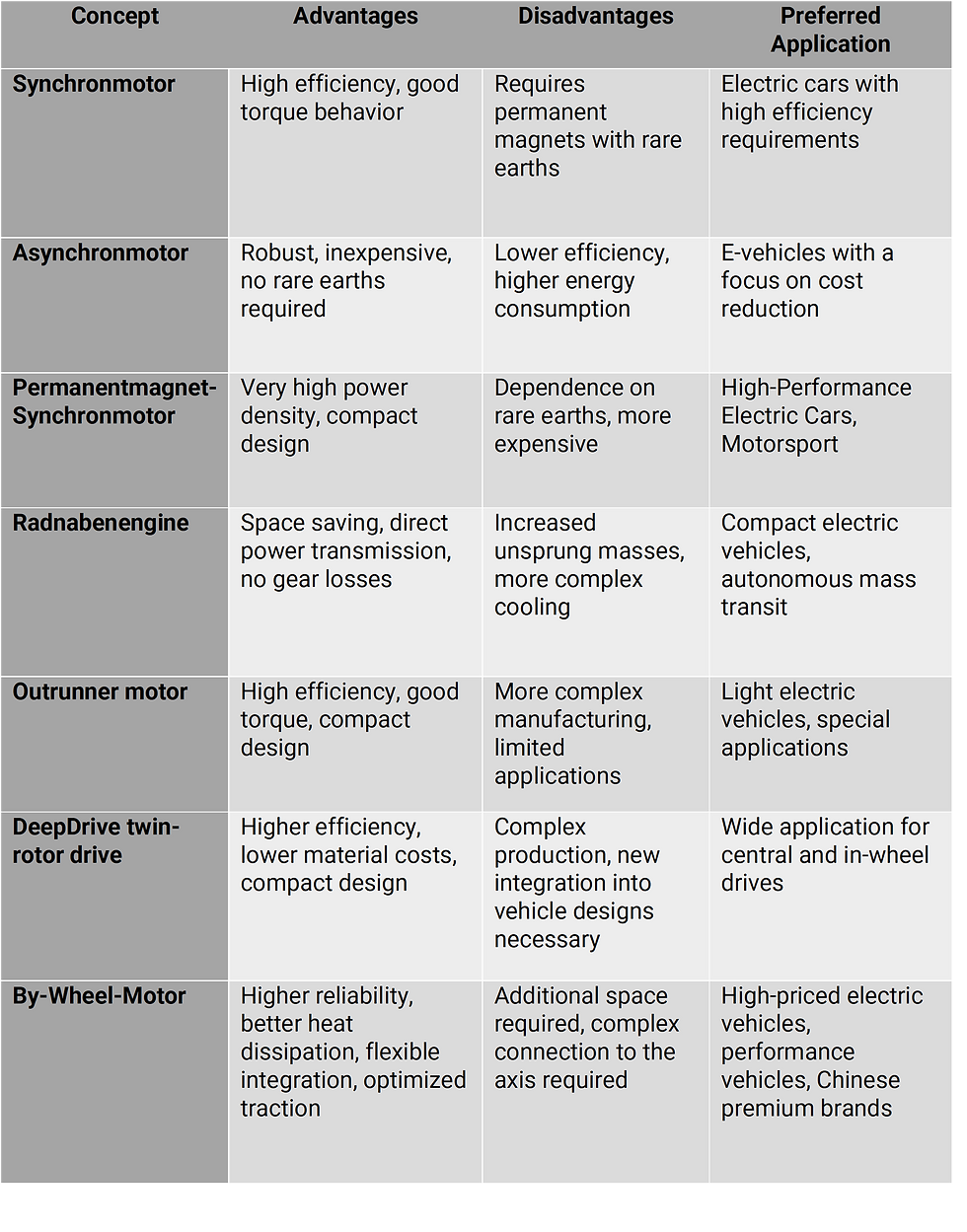
These different concepts show that electromobility is constantly evolving and provides a wide variety of solutions for different requirements. While classic in-wheel drives save weight and space by being integrated directly into the wheel, by-wheel motors offer better heat dissipation and robustness. DeepDrive, on the other hand, optimizes the use of efficiency and materials and could play a key role in electric vehicle construction in the future.
Comments