Electric motors without rare earths: Sustainable innovations for a resource-secure future
- Wolfgang A. Haggenmüller
- May 30
- 14 min read
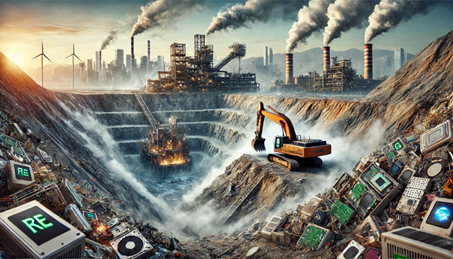
In the course of the global discussion about resource security and sustainability, the development of electric motors that do not require rare earths is increasingly becoming the focus of research and industry. The motivation to avoid rare earths is mainly based on concerns about a volatile supply chain, political dependencies and environmentally harmful mining practices. In particular, the automotive industry and wind energy, where electric motors are used on a large scale, are looking for alternative technologies that do not require the critical materials.
As early as the 1990s, the first research work began to deal with alternative magnetic materials and motor concepts. Traditional electric motors often rely on permanent magnets containing neodymium, dysprosium or terbium – all rare earths. These magnets offer high power densities and compact designs, but at significantly higher material costs and with long-term security of supply risks. It was clear early on that replacing these materials would be advantageous not only economically, but above all ecologically and geopolitically.
Why Rare Earths Should Be Avoided in Electric Motors: Scarcity of Resources, Environmental Impact and Economic Factors
The elimination of rare earths in electric motors is increasingly becoming an important goal in the research and development of modern drive systems. The reasons for this lie not only in ecological aspects, but also in geopolitical and economic challenges. Rare earths, especially neodymium, dysprosium, and terbium, are used for permanent magnet synchronous motors (PMSM), which are used in many electric vehicles and industrial applications. However, the extraction and processing of these materials entails considerable problems.
Resource Scarcity and Geopolitical Dependencies
Rare earths are paradoxically not so rare, but their economically usable deposits are concentrated in a few regions of the world. China controls about 60-70% of global production and owns large shares of global reserves. This monopoly position leads to significant risks for the supply chain. Political tensions, export restrictions or trade conflicts can quickly lead to supply bottlenecks and price fluctuations that could destabilize the entire electromobility industry.
In addition, the global demand for rare earths is growing drastically due to the increasing demand for electric vehicles, wind turbines and other high-tech products. According to forecasts, supply could already lag behind demand in the next few years, which will drive up prices further and make technological alternatives all the more attractive.
According to current estimates, the world's reserves of rare earths amount to about 130 million metric tons.
The distribution of these reserves is as follows:
China: 44 million metric tons
Brazil: 21 million metric tons
India: 6.9 million metric tons
Australia: 5.7 million metric tons
Russia: 3.8 million metric tons
Vietnam: 3.5 million metric tons
United States: 1.9 million metric tons
Greenland: 1.5 million metric tons
These figures make it clear that China is not only the largest producer, but also the country with the most extensive reserves of rare earths. This underlines China's importance in the global market for these critical raw materials.

If the demand for rare earths continues at an annual growth rate of 5%, the known global reserves would probably last until 2092 . After that, new deposits or recycling measures would be necessary to meet demand.
Environmental impact of mining and processing
The mining and refining of rare earths is associated with considerable ecological consequences. Rare earths usually do not occur in pure form, but are bound in ore mixtures that have to be chemically separated at great expense. This process requires large amounts of water, acids, and other chemicals, creating toxic residues.
One of the biggest problems is radioactive contamination by accompanying minerals such as thorium and uranium. In China, where a large proportion of rare earths are mined, inadequate environmental regulations mean that toxic waste often ends up in the environment. Entire regions in Inner Mongolia have been damaged by radioactive tailings piles and waters contaminated with heavy metals.
Another problem is the enormous energy requirement of processing. Since many of the separation processes take place at high temperatures and with intensive chemical processes, the production of magnetic materials contributes significantly to CO₂ emissions. The expansion of electromobility with such an environmentally harmful resource is therefore in contradiction to the actual objective of climate neutrality.
Economic challenges: costs and price fluctuations
In addition to ecological and geopolitical aspects, economic factors also play a central role. The price of rare earths is subject to strong fluctuations, which are influenced by political decisions and market manipulation. Neodymium and dysprosium in particular have experienced significant price jumps in recent years.
One example is China's decision in 2010 to drastically limit exports of rare earths. Within a few months, the prices of neodymium multiplied, forcing many companies to look for alternatives. Even if the markets calm down in the meantime, the risk remains that future trade conflicts or bottlenecks will lead to price shocks again.
For companies that rely on electric motors, this means not only rising production costs, but also uncertainties in long-term planning. Automotive manufacturers and industrial producers are therefore striving to become less dependent on these volatile raw material markets.
Technological alternatives and pressure to innovate
The need to do without rare earths has triggered a surge in innovation in electric motor development. Magnetless drive concepts such as reluctance motors or induction motors offer promising alternatives that do not require expensive and environmentally harmful materials.
Although such motor concepts have often been associated with disadvantages such as higher installation space, more complex control or lower efficiencies in the past, modern developments in power electronics, control technology and materials science have mitigated many of these challenges. Companies such as BMW, Renault and Tesla are already relying on such solutions to reduce their dependence on rare earths.
An additional advantage is the recyclability of magnetless motors. Permanent magnet motors are difficult to recycle because the magnets can only be recovered with great effort. Induction motors or reluctance motors, on the other hand, are mainly made of copper, iron and aluminium – materials that can be easily recycled.
A strategic decision for the future
The elimination of rare earths in electric motors is not just a technical challenge, but a strategic necessity for industry, the environment and society. The dependence on geopolitically sensitive raw materials, the massive ecological damage of mining and the economic risks of volatile commodity markets make a switch to alternative drive concepts inevitable.
The development of magnetless motors is progressing rapidly, and many manufacturers are already embracing these technologies. While there were technical limitations in the past, modern induction and reluctance motors are now more powerful, cost-efficient and sustainable than ever before.
The trend is clear: electric motors without rare earths will prevail in the long term and help to make electromobility and industrial applications more environmentally friendly, resource-saving and economically stable.
Development history and technological approaches
The development of alternative electric motors has spawned several technical paths. In addition to the further development of the classic asynchronous motor, which itself does not require permanent magnets, intensive research was carried out on switching winding and reluctance motors. These motor types use a basic magnetic principle based on changing magnetic fields without the use of specially alloyed permanent magnets. While in the past the asynchronous motor was often valued for simplicity and robustness, reluctance motors offer higher efficiency while reducing dependence on strategic raw materials.
In an interview, Dr. Klaus Ritter, senior engineer at a leading German automotive supplier, explained:
"The challenge is to achieve an equivalent level of performance without resorting to rare earths. However, modern control technologies and innovative materials make it possible for alternative engine concepts to steadily increase in performance."
Another approach is the hybridization of technologies, in which induction motors are combined with special geometries and optimized control algorithms to achieve a performance profile similar to that of permanent magnet motors. These motor solutions are already being tested in series production, albeit still in limited areas of application.
Structure and function
Magnetless drive systems are based on the principle that instead of permanent magnets, electromagnetically generated magnetic fields are used to generate torque. In contrast to conventional synchronous or permanent magnet motors, in which the magnetic flux density is primarily determined by fixed magnets, magnetless systems usually generate the required magnetic field by specifically controlling coils on the stator. Two technical concepts are usually used: the induction-based drive and the switchable reluctance motor.
Induction-based systems
Principle:
In an induction-based motor concept, a rotating magnetic field is generated in the stator, which is generated by alternating current via multiphase windings. This rotating magnetic field induces eddy currents in a conductive rotor, which build up their own magnetic field due to the electromagnetic induction principle. The torque is generated by the interaction between the field created on the stator side and the induced rotor-side field.
Construction:
Stator:
The stator contains multi-phase windings that are arranged symmetrically around the motor. These windings are controlled by an inverter that generates a rotating magnetic field by phase shift.
Rotor:
In many cases, the rotor consists of a conductor (such as a squirrel cage rotor in asynchronous motors) or of a design element that reacts specifically to induced currents. In magnetless systems, conductive aluminum elements or special copper rotors can also be used to maximize the induced current flow.
Control electronics:
Modern control systems ensure that the frequency and amplitude of the alternating currents are adjusted to enable precise control of the rotating field. This allows variable speed control and the optimization of efficiency.
Principle sketch (induction-based):

In this schematic diagram it becomes clear that the constantly rotating magnetic field in the stator (through cyclically switched coils) causes an induced current in the conductor rotor, which in turn then supplies the necessary torque.
Switchable reluctance motors
Principle:
The switchable reluctance motor (SRM) uses the property that the magnetic resistance (reluctance) in a magnetic circuit depends on the relative position of the magnetic components. The rotor has a multi-pronged, often solid core without permanent magnetic properties. The stator poles are excited sequentially, so that the rotor-side element is always pulled into the position of the lowest reluctance – i.e. the strongest magnetic connection. This principle of "attraction" leads to a gradual movement of the rotor.
Construction:
Stator:
The stator of an SRM has a pronounced segmentation in the form of magnetically conductive iron blocks, which are activated by targeted windings. Usually, these poles are designed in an exact, regular arrangement to allow for uniform rotation.
Rotor:
In contrast to the permanent magnet motor, the rotor is made exclusively of iron, which offers variable magnetic resistance due to its geometric arrangement (salience). The rotor shape is optimized so that it runs as quickly as possible to the activated stator teeth.
Control electronics:
The control logic for an SRM is particularly complex, as the ignition of the stator windings must be precisely timed in order to be synchronous with the natural "tightening behavior" of the rotor. Modern microcontrollers and high-performance sensors for angle determination are used here.
Principle sketch (reluctance motor):
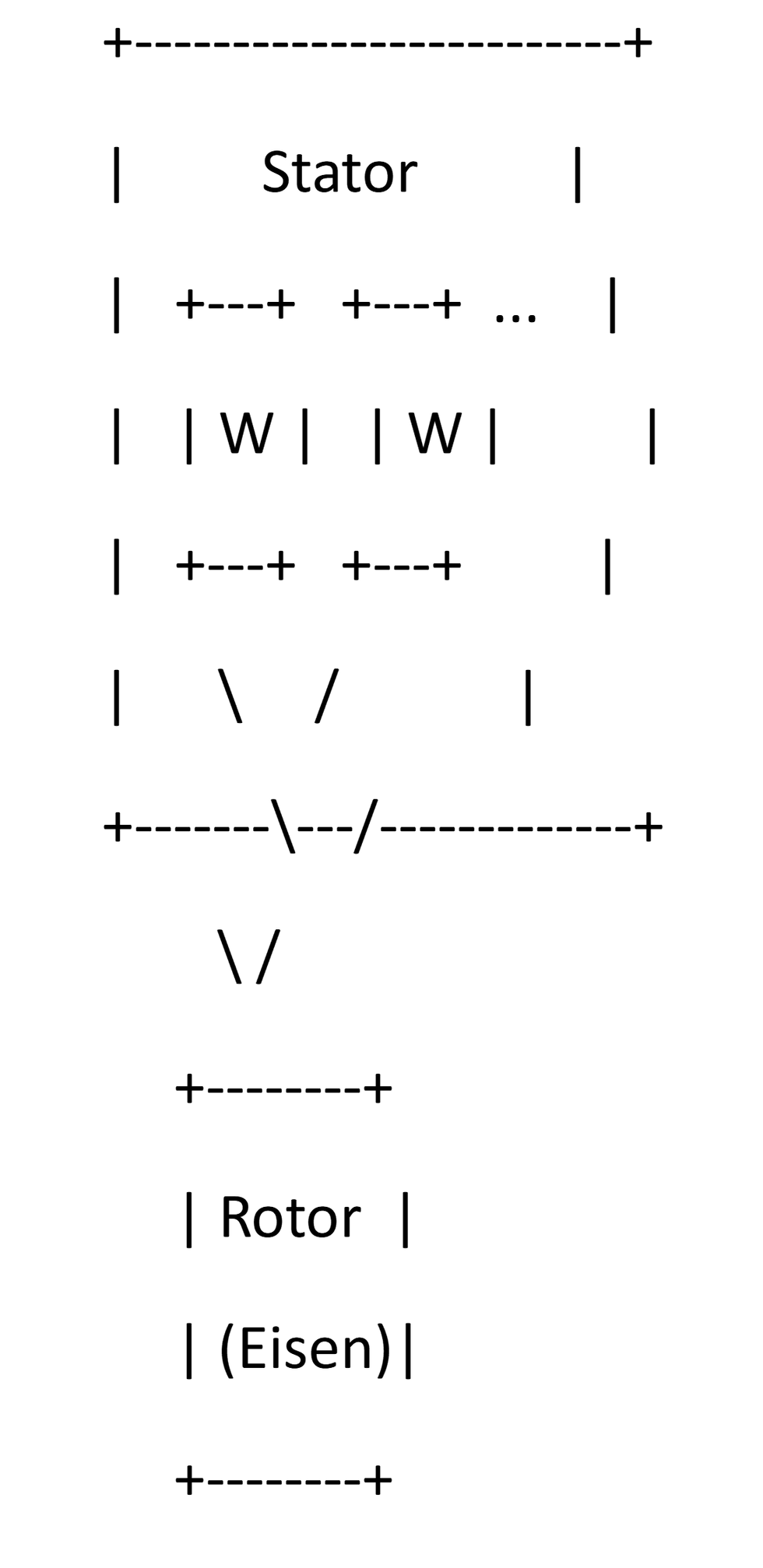
This diagram shows that the poles of the stator are magnetized one after the other by targeted activation of the windings. The rotor reacts to these changing "magnetic poles" and moves due to the force to bring itself into the position of lowest magnetic reluctance.
Technical challenges and optimization
With both concepts – induction-based drive technology and the switchable reluctance motor – engineers face a number of key challenges:
Control accuracy:
The precise control of the magnetic fields requires very fine control of the current pulses. Modern signal processing and power electronics solutions are indispensable here.
Thermal management:
The lack of permanent magnets shifts the thermal load to the windings and conductive parts of the motor. Optimising heat cooling and thermal distribution is therefore crucial to minimise efficiency losses.
Material optimization:
The rotor and stator require not only conductive but also highly permeable materials that allow a fast magnetic response while minimizing energy loss.
Magnetless drive systems offer a number of advantages by eliminating the need for critical permanent magnets, especially in terms of security of supply and material costs. Technically, primarily induction-based systems and switchable reluctance motors are used. Both approaches aim to achieve the same or similar torque as conventional motors through targeted electromagnetic excitation and precise control. Principal sketches illustrate the basic structure: While in the induction-based motor a rotating magnetic field in a stator arrangement causes current induction in the rotor, the reluctance motor works with sequential activation of stator poles to pull the rotor into the position of the lowest magnetic resistances.
Continuous research and development in this field aims to improve control accuracy, overcome thermal challenges and ultimately transfer technical innovations into industrial series applications.
Current status and applications
Today, there are already several prototypes and even the first series applications of electric motors without rare earths. For example, European car manufacturers are experimenting with induction-based drive systems to be used in electric vehicles. Alternative technologies are also increasingly being tested in pilot plants in the field of industrial drives. According to a report by the Fraunhofer Institute, the development of reluctance motors is on the verge of a breakthrough on a commercial scale – a milestone that could significantly reduce dependence on critical raw materials.
Prof. Dr. Martina Huber, expert in electrical machines at the Technical University of Munich, added:
"The new developments make it possible to rely on alternative technologies even in industrial sectors that require high power densities. The optimization of the magnetic circuit and the digitalization of the drive technology are key components in this process."
Application examples that are already moving into series production are mainly found in areas where safety and independence from critical materials are crucial. Some manufacturers are already increasingly relying on induction motors in power tools and conveyor systems, while pilot projects with magnetless systems are being tested in the automotive sector.
There are already vehicles or vehicle projects that are equipped with electric motors without the use of rare earths or whose manufacturers are actively working on such solutions:
Tesla: The company has announced that it will use electric motors in future vehicles without the use of rare earths.Mugglehead Investment Magazine
Nissan: The Japanese automaker is developing new electric motors based on samarium instead of neodymium to reduce dependence on rare earths.Auto Motor und Sport
Renault: In cooperation with Valeo and Valeo Siemens eAutomotive, Renault plans to develop electric motors for passenger cars that do not require rare earths. Production of these engines is scheduled to start in France in 2027.ELECTRONICS PRACTICE
BMW: BMW uses externally excited synchronous motors in some of its electric vehicles, which do not require permanent magnets and thus rare earths.DIE WELT+1ingenieur.de+1
These developments aim to reduce dependence on rare earths and create greener and more cost-efficient alternatives to electric motors.
Nevertheless, the number of motors used in automobiles will continue to be predominantly electric motors with rare earths in the foreseeable future.

Comparison: Electric motors without rare earths vs. conventional electric motors
The following is a tabular overview that summarizes the main differences between the two technologies:
Property | Engines without rare earths | Conventional electric motors (with rare earths) |
Material dependence | No or less demand for critical and sometimes geopolitically controversial materials | High demand for rare earth materials (neodymium, dysprosium, etc.) |
Power density | Traditionally lower power density, but continuous improvements through optimized designs and control algorithms | Very high power density thanks to strong permanent magnets |
Efficiency | Now almost competitive, depending on circuit optimizations and special controls | High efficiency already established, but potentially limited by material shortages |
Cost | Development costs increase due to the need for innovative solutions, but often more economical in the long term due to more stable supply chains | High material costs and price fluctuations due to market situations |
Manufacturing processes | Some require switching to new manufacturing processes and manufacturing technologies, which requires initial investment | Established production processes, but dependent on international suppliers |
Environmental aspects | Lower ecological impact in raw material extraction, potentially more sustainable in the life cycle | Significantly more polluting in the mining and processing of rare earths, often associated with problematic recycling processes |
Technology maturity | Intensive research and development phase, first pilot series and test applications available in industrial and automotive sectors | Very mature, established in almost all areas of application |
Economical scalability | Long-term potential for cost reduction if series production and process optimization take effect. Currently still in the transition phase | Scaling already fully realized, but always susceptible to commodity price fluctuations |
Technical and economic differences
From a technical point of view, the difference lies primarily in the design principle: Induction or reluctance-based concepts are often used for engines without rare earths. Although these currently offer lower power densities, they benefit from continuous advances in control engineering and materials research. From an economic point of view, reducing dependence on strongly fluctuating raw material prices offers enormous potential for long-term cost advantages. However, investments in new manufacturing technologies and process optimizations are first necessary to achieve economies of scale.
Outlook and challenges
The current progress in the development of magnetless electric motors marks an important milestone in electromobility and industrial drive technology. The industry is watching the developments closely, as widespread use can not only mean economic relief, but also an ecological gain. In addition to optimizing power density and efficiency, the challenges include integration into existing control systems and adaptation of manufacturing technologies. However, initial series applications in less demanding environments indicate that a broad market entry in the next ten years is quite realistic.
In conclusion, it can be said that electric motors without rare earths represent a forward-looking alternative that not only means technological innovations, but also strategic risk reduction for the economy. Their further development is thus intensively pursued both in research and in industrial applications – always with the aim of overcoming the limits of conventional technologies and promoting sustainable, economical solutions. This compilation shows how the transition to engine drive solutions without rare earths is seen as a strategic step in the context of sustainability and security of supply – with significant advantages, but also technical and cost-related challenges that need to be overcome
Projects on magnetless drives
As part of the search for alternative drive technologies without the use of rare earths, there are several interesting development projects worldwide that focus on the use of magnetless or reluctance-based electric motors. Below are some of these projects, their current status, results achieved and the next steps.
Fraunhofer Project "Magnetless Drive Systems"
In recent years, the Fraunhofer Institute has worked intensively on the development of electric motors that do not require permanent magnets. The aim of the project is to achieve performance profiles comparable to those of conventional engines through innovative control techniques and optimized geometries. In an expert discussion, a senior developer at the institute reported:
"By using novel material combinations and digital control algorithms, we were able to achieve an efficiency that comes close to that of conventional drive solutions even in prototypes."
Current project status:
Phase: Pilot phase with successful prototype tests in laboratory environments and first field tests in industrial applications.
Results: Demonstrable performance and stability in operation, but there are still challenges in miniaturization and integration into existing vehicle or drive systems.
Next steps: Further development of manufacturing processes and scaling of the technology, especially in cooperation with automotive manufacturers and suppliers.
VDMA initiative "RENA – Reluctance Motors for Electromobility"
Another important initiative comes from the German Engineering Federation (VDMA), which initiated the RENA project. The goal is to develop reluctance motors that are cost-efficient and sustainable by eliminating the use of rare earths. A spokesperson for the project explained in an industry interview:
"Our analyses show that reluctance motors can be a reliable alternative in the future, especially when looking at the entire value chain. The first prototypes already meet many of the required performance parameters."
Current project status:
Phase: Development phase – from laboratory prototypes to initial test series in real-world application environments, such as power tools and small commercial vehicles.
Results: Initial test series have shown that the motors are competitive in terms of energy efficiency and robustness.
Next steps: Optimization of the design for series production, extensive field tests and the adaptation of existing production processes.
European Consortium "AltDrive"
At the European level, there is the "AltDrive" consortium, which is made up of several research institutions and industrial partners. The aim of the project is to research novel electric motors that do not require any critical raw materials at all and to use them in areas such as industrial automation. The project publication stated:
"AltDrive represents a forward-looking collaboration that integrates the entire supply chain from basic research to industrial application. This enables us to fully exploit technological potential without dependence on rare earths."
Current project status:
Phase: Concept validation and prototype development – first demonstrators have been successfully tested in laboratory environments.
Results: Significant progress in the optimization of circuit and control technology, but still in an early phase with regard to integration into large-scale production.
Next steps: Integration into pilot plants as well as extensive field trials in industrial environments to test scalability and long-term stability.
Summary and outlook
The above-mentioned projects show that the global research and development pressure regarding electric motors without rare earths is great. Key objectives include:
Technological innovation: Development of novel design principles (e.g. reluctance motors and induction-based concepts) that are intended to achieve a power density comparable to conventional motors.
Economic sustainability: Reduction of dependence on critical and price-sensitive raw materials, which can lead to more stable production costs in the long term.
Industrial integration: Initial prototypes and pilot projects are already showing positive results, which are now being further developed towards series production.
Experts such as representatives of the Fraunhofer Institute and VDMA emphasize that the next steps lie primarily in scaling and adapting existing manufacturing processes. While the laboratory results are promising, it is now important to transfer the technologies to an industrial scale and successfully integrate them into series applications.
Sources and further reading:
These projects represent the progress to date and future prospects in the development of electric motors without the use of rare earths – a key area that promises technological, economic and environmental benefits.
Sources and further reading:
Fraunhofer Institute for Manufacturing Engineering and Automation – Reports and Research Projects on Sustainable Engine Technology
Interviews with experts such as Dr. Klaus Ritter and Prof. Dr. Martina Huber (published interviews in journals and conference proceedings)
Publications in trade journals on alternative electric motors and new manufacturing technologies (VDMA Reports, IEEE publications)
Fraunhofer Institute for Manufacturing Engineering and Automation – Research projects on magnetless drive systems
VDMA publications on alternative electric motors and the RENA project
Project publications and interviews within the framework of the European consortium "AltDrive"
Comments