Additive manufacturing: Revolutionizing metal production for the future of industry
- Wolfgang A. Haggenmüller
- Oct 23, 2024
- 12 min read
Additive manufacturing of metal parts is revolutionizing industrial production through innovative technologies such as Direct Metal Laser Sintering (DMLS) and Selective Laser Melting (SLM). These processes enable the production of complex geometries that would be difficult to achieve with traditional methods, reducing material waste and production costs. Despite initial challenges, such as high costs and slow production speeds, the technology in the Gartner Hype Cycle is transitioning from the "valley of disappointment" to the "path to enlightenment". To unleash its full potential, cost reductions, automated post-processing and faster production must be achieved. Leading suppliers such as GE Additive, EOS and SLM Solutions are driving these developments and offering solutions for the aerospace, automotive and medical industries. Groundbreaking examples, such as the 3D printing of turbine blisks and rocket engine parts, demonstrate the immense potential of this technology.

3D Printing and Additive Manufacturing of Metal Parts: Basics, Applications, Processes and Market Development
Additive manufacturing, often referred to as 3D printing, has developed rapidly in recent years and is a pioneering approach in the production of metal parts. Unlike traditional manufacturing processes such as milling or casting, where material is removed or poured into molds, additive manufacturing is done by applying material layer by layer to create the desired component. This article sheds light on the technical basics, the possible applications, various processes, their advantages and disadvantages as well as the historical and future market development.
Processes and technologies
There are various processes in additive manufacturing that differ in terms of precision, material use and areas of application. 3D printing of metal parts is based on the layer-by-layer structure of a workpiece. In this process, metal powders or wires are melted by energy sources such as lasers, electron beams or electric arcs and applied in a targeted manner. In additive manufacturing, a distinction is made between different techniques, which differ depending on the energy source used and the type of material used. One of the most common techniques is the powder bed fusion process. In this process, metal powder is evenly distributed on a build platform and selectively melted by a laser or electron beam. Another layer of powder is applied, and the process is repeated until the component is completed. In addition, there are processes such as direct energy deposition, in which the metal powder is injected directly into the melting area, and binder jetting, in which a binder is applied to powder and then sintered.
Selective Laser Melting (SLM):
Advantages: Very high precision, density and strength of the workpiece.
Disadvantages: High energy consumption, long production times for larger components.
Applications: Aerospace, medical technology.
Electron beam melting (EBM):
Advantages: Faster than SLM, lower material stresses in the final product.
Disadvantages: Lower precision, post-processing often necessary.
Applications: Applications where high strength and weight saving are important.
Binder Jetting:
Advantages: High production speed, low cost of mass production.
Disadvantages: Mechanical properties of the parts are lower, requires post-processing.
Applications: Prototyping, mass production of simple parts.
Direct Metal Laser Sinter (DMLS):
Advantages: Suitable for complex geometries and smaller series.
Cons: Relatively slow production speed.
Applications: Automotive, tools and prototypes.
Areas of application of additive manufacturing
Additive manufacturing of metal parts is used in various industries, especially in areas where traditional manufacturing processes are limited by complex geometries, cost, or production speed. Important areas of application are:
Aerospace industry: Complex, lightweight, yet high-strength parts used in engines and structural components.
Automotive industry: Lightweight components for electric vehicles and custom-made products for motorsport applications.
Medical technology: Manufacture of implants, prostheses and surgical tools that can be individually adapted to patients.
Tooling and Prototyping: Rapid production of functional prototypes and tools.
History of Additive Manufacturing
The first approaches to additive manufacturing date back to the 1980s. The technology was originally developed for the rapid production of prototypes. In the 1990s, companies began to develop processes for metal processing, but it was not until the 2000s that metallic 3D printing processes became established in industry. Advances in laser technology and materials science have driven this development, so that metal parts can now be mass-produced.
Market development and cost structure
The market size for additive manufacturing is growing rapidly. In 2020, the global market value was about $12 billion and is expected to rise to over $30 billion by 2025. However, the cost of 3D printing processes is still comparatively high, especially in terms of the starting material (metal powder) and the energy required. Nevertheless, additive manufacturing has considerable potential due to falling costs for machines and materials as well as increasing production speeds.
Production speed is a critical factor that has improved in recent years. This is where Moore's Law comes into play: Similar to the semiconductor industry, we see a doubling of efficiency and speed in additive manufacturing technology every two to three years. This tendency leads to a continuous reduction in production costs.
Cost reduction through Moore's Law
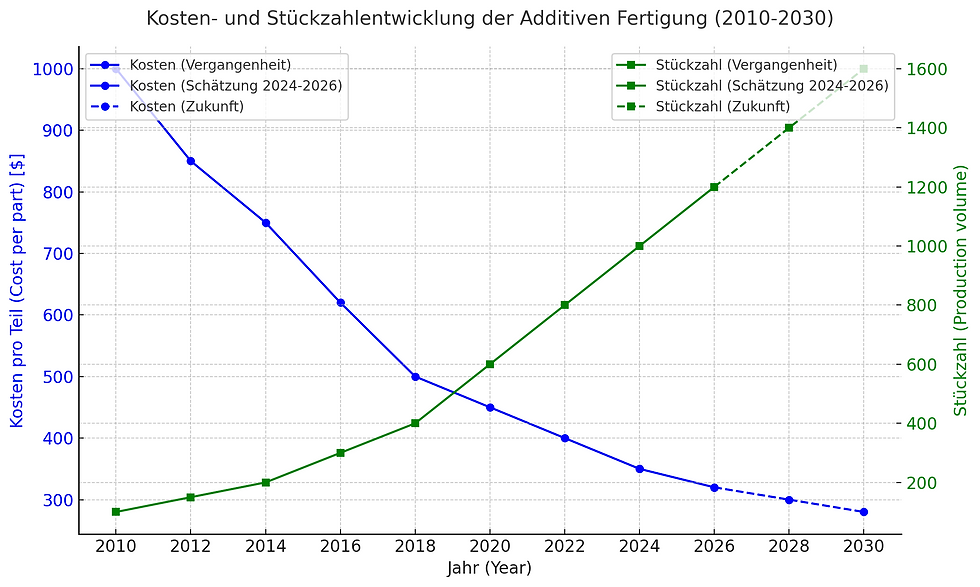
The chart shows the steady decline in the price of additive manufacturing due to technological advances and efficiency gains. It shows the price decline per component in recent years and a forecast for future development up to 2030. The decreasing costs are an indication of increasing efficiency and advancing technological developments, which are promoted by effects similar to Moore's Law.
Additive manufacturing of components
There are several factors to consider when it comes to additive manufacturing of metal parts, especially when it comes to replacing existing components that are traditionally manufactured by machining or forming technology with additive processes. While additive manufacturing offers advantages such as complex geometries that are difficult to achieve with conventional methods, there are also limitations. For example, components for additive processes often have to be rethought, as this technology is based more on the layer-by-layer structure of material. This means that when designing metal parts, care must be taken to include support structures for overhanging elements that will need to be removed later, which adds to the effort. A simple one-to-one transfer of existing designs from machining or forming production is therefore often not possible without making significant adjustments.
Another design feature is the topic of wall thicknesses and cavities. Additive processes allow the design of cavities or internal channels, which is impossible or difficult to implement with other manufacturing processes. Nevertheless, the stresses that arise when the material cools down, which can lead to warping or cracking, must be taken into account. This requires special design measures to ensure component quality.
The quality of additively manufactured metal parts can be high, but it is highly dependent on the materials used, machine precision, and process parameters. The surface finish is usually worse than that of machined parts and often requires post-processing. In terms of mechanical properties, additively manufactured parts can compete with conventionally manufactured parts, especially when post-treatments such as heat treatment or hot isostatic pressing (HIP) are applied. Nevertheless, it must be borne in mind that the anisotropic behavior of additively manufactured parts – i.e. the different strength in different directions due to the layer structure – can become a challenge.
In summary, additive manufacturing opens up many new design possibilities, but direct adoption of existing designs is not possible without adjustments. Precise knowledge of the process parameters and material properties is required to ensure high quality.
SWOT Analysis of Additive Manufacturing
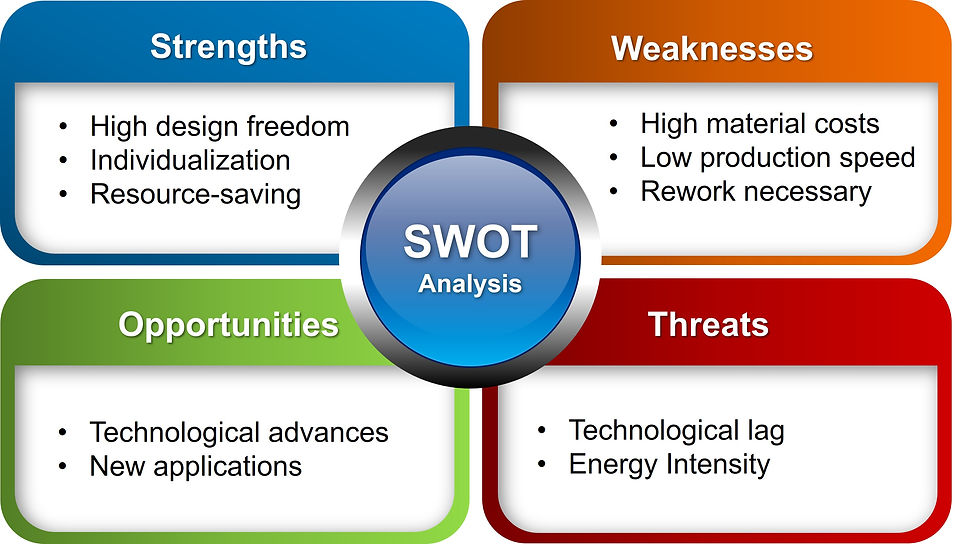
Strengthen:
High design freedom: Complex geometries can be realized that would be impossible with traditional processes.
Individualization: High flexibility in the production of individual pieces and small series.
Resource-saving: Minimization of material waste compared to subtractive processes.
Weaken:
High material costs: Metal powder is expensive and often difficult to obtain.
Low production speed: Even slower than conventional processes in mass production.
Post-processing necessary: Many metal parts still need to be machined after printing to achieve the desired surface quality and strength.
Odds:
Technological advancements: Improved machinery and materials will increase production speed and reduce costs.
New applications: Increasing design freedom is opening up new fields of application, e.g. in medical technology and automotive engineering.
Risks:
Technological lag: Companies that do not invest in additive manufacturing could fall behind in the competition.
Energy intensity: The high energy requirements of the processes could become problematic in view of rising energy prices.
Position of Additive Manufacturing in the Gartner Hype Cycle
Additive manufacturing, especially that of metal parts, goes through the Gartner Hype Cycle, which presents technological innovations and their acceptance to provide guidance to companies and investors as to where a technology stands in the development and maturation process. The Hype Cycle consists of five phases:
Technological trigger (innovation trigger): This is where the technology is discovered for the first time and the first experiments and concepts are created.
Peak of Inflated Expectations: Technology comes into the media spotlight, and exaggerated expectations are raised.
Trough of Disillusionment: The technology does not immediately achieve the results hoped for, and the hype decreases.
Slope of Enlightenment: Real-world applications emerge and technology matures.
Plateau of Productivity: The technology is established and market penetration is reaching a high level.
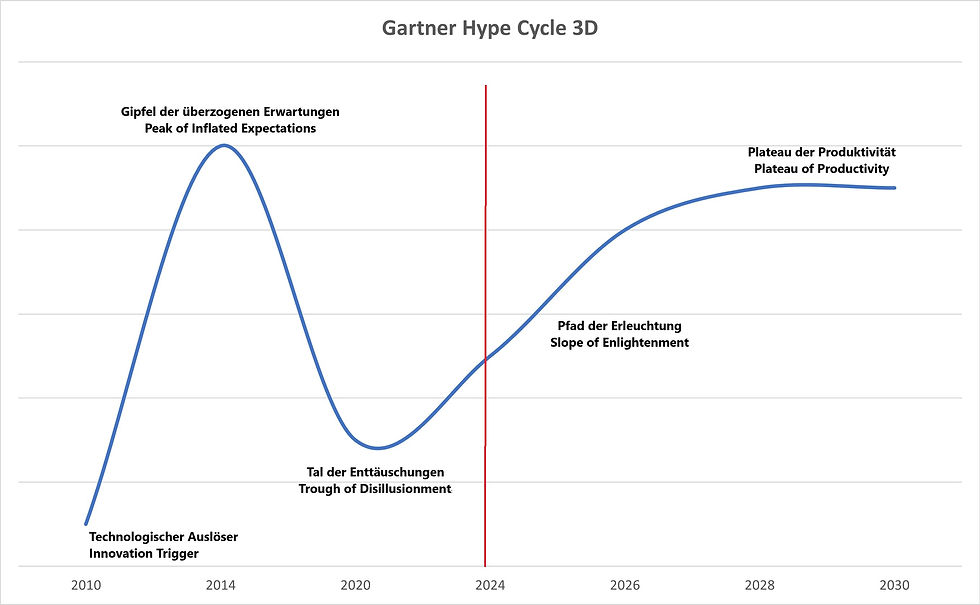
Currently, the additive manufacturing of metal parts is in the transition from the "valley of disappointments" to the "path of enlightenment". In the early 2010s, 3D printing was heavily hyped and many expected a complete revolution in manufacturing. However, the technology reached its limits, especially in terms of production speed, costs and material properties. After a period of disappointment in the late 2010s, we are now in a phase where the technology is finding concrete applications and has made significant progress.
Why in the "Path of Enlightenment"?
Exaggerated expectations: A few years ago, when additive manufacturing began to become mainstream, there was a tremendous amount of enthusiasm and expectations, especially regarding the ability to revolutionize entire industries. The technology promised to replace traditional manufacturing methods, primarily through its ability to create complex geometries and minimize material waste. Reality of the challenges: In recent years, however, the real challenges have become apparent: high costs, slow production speed and the need to extensively post-process components in order to achieve the required tolerances and surface qualities. These hurdles led to disillusionment in the industry, which led the system into the "valley of disappointments".
Maturity of the technology: The most important processes such as selective laser melting (SLM) or electron beam melting (EBM) have gained in precision and efficiency. They are already an integral part of production processes in industries such as aerospace and medical technology. Availability of materials: The range of usable materials has expanded, which increases production possibilities. Cost reductions and efficiency gains: Due to technical advances and better machines, 3D printing of metal parts has become economically viable in some areas. Real-world industrial applications: Additive manufacturing is used for complex and customized components that would not be economically feasible or impossible to manufacture using conventional processes.
Prerequisites for the next steps Path of Enlightenment and Plateau of Productivity
In order to successfully complete the next step towards the "Path of Enlightenment", the following conditions must be met:
Cost reduction and material diversity: Advances in material development (e.g. cheaper metal powders) and more efficient machines must make production cheaper and more accessible.
Automated post-processing: At the moment, post-processing of 3D-printed metal parts is time-consuming and costly. The next step requires automated processes that minimize this challenge.
Increased production speed: Production time must be further optimized to make the technology usable for mass production.
Standardization: Uniform quality standards and certifications, especially in the field of aviation and medicine, are necessary to promote broad industrial application.
Integration into existing manufacturing processes: Additive manufacturing must be established as a complementary technology that coexists with and complements existing manufacturing processes such as milling and casting.
Provider
These suppliers are among the leaders in metal additive manufacturing and are driving the technology forward through innovation and specialization in various industries.
GE Additive
GE Additive invests heavily in the advancement of metal 3D printing technologies, particularly for the production of complex components such as turbine blisks and printed parts for aircraft engines.
Origin: USA
Founded: 2016 (part of the General Electric Group)
Technology: GE Additive offers technologies such as Direct Metal Laser Melting (DMLM) and Electron Beam Melting (EBM).
Products: Machines such as the Arcam EBM and Concept Laser systems.
Areas of application: Mainly in aerospace, medical, automotive and energy.
EOS (Electro Optical Systems)
EOS was one of the first companies to commercially use industrial 3D printers for metals. It is one of the pioneers in the standardization of additive manufacturing processes.
Origin: Germany
Founded: 1989
Technology: Leader in laser sintering technology. For metal parts, EOS uses the DMLS (Direct Metal Laser Sintering) process.
Products: Machines such as the EOS M 290 and EOS M 400 for metal 3D printing.
Areas of application: Aerospace, automotive, medical technology, toolmaking and more.
SLM Solutions
SLM Solutions is considered one of the market leaders in the development of metal 3D printing systems. Their machines are known for their ability to use multiple lasers at the same time, which increases productivity.
Origin: Germany
Founded: 2006
Technology: Develops selective laser melting (SLM) machines for 3D printing metal parts.
Products: The SLM®500 and SLM®800 machines, which are designed for the industrial production of metal parts.
Areas of application: Automotive industry, aviation, healthcare, toolmaking, energy.
Renishaw
Renishaw has focused heavily on the manufacture of high-end metal parts, particularly in the medical sector, where precise and complex parts are required.
Origin: Great Britain
Founded: 1973
Technology: Renishaw uses Laser Powder Bed Fusion (LPBF) to produce metal parts.
Products: RenAM 500Q is one of the main machines specially designed for the production of metal parts.
Areas of application: Mainly in the healthcare sector (dentistry, orthopaedics), aviation, precision engineering.
3D Systems
3D Systems was one of the first companies to develop 3D printing. It offers a wide range of applications for metal and plastic parts.
Origin: USA
Founded: 1986
Technology: Uses Direct Metal Printing (DMP), a laser-based process for melting metal powder.
Products: ProX DMP 320, one of the flagship machines designed for metal processing.
Areas of application: Healthcare, aviation, automotive industry, energy.
Trumpf
Trumpf is a leading manufacturer of laser technologies and has established itself strongly in additive manufacturing in recent years. They combine additive manufacturing with classic machining techniques.
Origin: Germany
Founded: 1923
Technologie: Laser Metal Fusion (LMF) und Laser Metal Deposition (LMD).
Products: Machines such as TruPrint 1000 and TruPrint 5000.
Areas of application: Medical technology, automotive industry, aviation, tools and mold making.
Desktop Metal
Desktop Metal focuses on the democratization of metal 3D printing and develops systems that are also accessible to small and medium-sized companies.
Origin: USA
Founded: 2015
Technology: Desktop Metal offers the Bound Metal Deposition (BMD) process, a variation of metal 3D printing aimed at mass production.
Products: Studio System and Production System, especially for small and mass production.
Areas of application: toolmaking, consumer goods, automotive industry, electronics.
Additive Industries
Additive Industries stands out for its highly automated systems that are designed for high productivity and make the 3D printing of metal parts more efficient.
Origin: Netherlands
Founded: 2012
Technology: MetalFAB1 is their main product, which provides an automated production system for the production of metal parts.
Areas of application: aerospace, automotive, high-tech industries.
Velo3D
Velo3D has built a reputation for its ability to print parts with minimal support structure, which is especially beneficial when manufacturing complex geometries in aviation.
Origin: USA
Founded: 2014
Technology: Develops the Sapphire® systems based on Laser Powder Bed Fusion (LPBF).
Products: Sapphire® is Velo3D's flagship system, providing support for complex geometries and challenging materials.
Areas of application: aerospace, energy, defense industry.
Prominent examples of metal parts produced by additive manufacturing
There are some groundbreaking examples that show the special advantages and potential of additive manufacturing of metal parts
LEAP Turbine Blisks (GE Aviation)General Electric Aviation uses additive manufacturing techniques to produce blade integrated disks (blisks) for the LEAP engines, which are widely used in the aerospace industry. The blisks are made from a special nickel alloy powder by means of selective laser melting. The components have a complex geometry that would be difficult to achieve with conventional manufacturing processes. Advantages: The nozzles are 25% lighter, consist of a single part (instead of 18 individual parts), which simplifies assembly and maintenance. In addition, they have a longer service life, have to withstand high thermal and mechanical loads and are more efficient in operation, which reduces fuel consumption.
Raptor engine parts (SpaceX)SpaceX prints central parts of its Raptor engine for the Starship rocket from a superalloy. These parts can withstand extreme temperatures and pressures that occur in the engines. The advantages are the shorter production times, as the parts are printed directly from CAD data and only have to be minimally post-processed. The engine is used for manned space projects, which is why the requirements for quality and safety are extremely high.
Titanium brake calipers (Bugatti)The luxury car manufacturer Bugatti produces brake calipers for the Chiron super sports car using titanium 3D printing. A significant weight reduction and at the same time higher strength compared to conventional methods. The process not only saves weight, but also allows the production of components with a unique geometric complexity.
Structural components for aircraft (Airbus)Airbus uses 3D printing for various metal components, including cabin parts and structural components. These parts are particularly light and yet strong, which leads to a reduction in fuel consumption and emissions. By using lightweight construction with 3D-printed metal parts, Airbus can increase aircraft efficiency and reduce operating costs.
Medical implants: Titanium implantsIn medical technology, 3D-printed titanium implants are manufactured for orthopedic use (e.g. hip or knee joints). These implants can be individually adapted to the patient and offer better integration with the bone. The implants are biocompatible and, due to the porosity of the printed structure, are able to grow better into the bone tissue, which promotes healing and stability.
Result
Additive manufacturing of metal parts has the potential to revolutionize many industries. Although cost and production speed are still challenges today, technological advances and efficiency gains will lead to further adoption of this technology. The market shows tremendous growth potential, and companies that invest in this area will be able to secure a competitive advantage.
Additive manufacturing of metal parts is on a promising path and has left the phase of initial hype-related exaggerations behind it. However, in order to take the next step towards mass production and industrial standardization, technological improvements are necessary. Above all, reducing costs and increasing speed will be crucial to take the technology to the "plateau of productivity".
Comments